Il existe de nombreuses définitions du terme « automatisation ». L’automatisation est une discipline, une fonction, un ensemble de technologies… Ce sont toutes des définitions correctes, mais elles expliquent toujours trop ou pas assez.
Commencez à partir d’ici. Le terme automatisation est né pour identifier tout ce qui est nécessaire pour faire fonctionner une machine (ou un processus) automatiquement, c’est-à-dire sans intervention humaine. L’automatisation industrielle, en particulier, exploite les technologies mécaniques, électroniques et informatiques pour le contrôle des processus de production industrielle, régissant les flux d’énergie, de matériaux et d’informations.
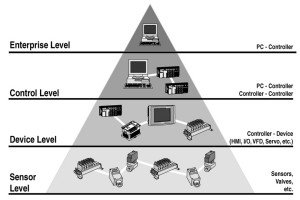
D’un point de vue historique, l’automatisation est née dans le but principal de remplacer l’homme dans les tâches répétitives ou nuisibles, par des équipements capables de fonctionner de manière autonome ou avec des interventions minimales de l’opérateur humain.
En fusionnant les technologies industrielles des processus de production et les technologies de l’information, elle vise à permettre la gestion efficace de l’information, se plaçant comme une branche de l’ingénierie moderne qui vise à réduire ou supprimer l’intervention humaine dans la production de biens et de services.
Comment un système d’automatisation est fait
Un système d’automatisation peut être décrit comme une pyramide (modèle CIM) dans laquelle différents niveaux peuvent être identifiés qui partent de la base du système, qui est le processus à contrôler, et atteignent les structures commerciales générales. L’une des versions les plus répandues de la pyramide CIM distingue quatre niveaux : le « champ », c’est-à-dire le lieu où se trouvent les processus à contrôler et les capteurs ; le « contrôle », où se trouvent les dispositifs d’automatisation tels que les régulateurs, les contrôleurs, les IHM locales, etc. ; « supervision » avec des PC et des systèmes chargés de la surveillance ; le niveau « entreprise » où résident les autres activités de l’entreprise.
Sur la base des fonctions exécutées dans les systèmes de production, trois types de composants de base d’un système d’automatisation peuvent être identifiés : les capteurs , qui ont pour objectif la mesure de quantités d’intérêt pour évaluer l’avancement et/ou la bonne exécution du travail dans le progrès; les transformateurs , qui, sur la base des mesures fournies par les capteurs et des objectifs des travaux en cours, décident des actions à entreprendre les actionneurs , qui exécutent les actions commandées par les organes de traitement.
Les méthodologies d’automatisation offrent les outils pour concevoir, en termes abstraits et formels, les algorithmes que les organismes de traitement utiliseront pour décider des actions à exercer sur l’installation à automatiser ; l’ automatisation technique concerne plutôt le développement de dispositifs physiques pour construire des capteurs, des actionneurs et des processeurs.
Un clin d’oeil à l’histoire
Le précurseur des systèmes d’automatisation peut être considéré comme le régulateur de vitesse de J. Watt (fin XVIIIe siècle) pour les locomotives à vapeur, dont le but initial était de maintenir leur vitesse constante, quel que soit le poids remorqué ou les pentes de la voie ferrée. Le régulateur, basé sur la vitesse réelle et la comparant mécaniquement à celle prédéterminée, a pu obtenir la puissance nécessaire pour faire varier la vitesse.
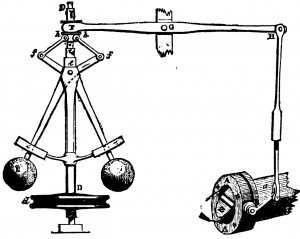
Régulateur de vitesse de J. Watt
Les automatismes modernes sont nés à la fin du siècle suivant, à l’époque de la révolution industrielle et des machines à vapeur, de la nécessité de disposer de machines toujours plus rapides et précises. Il fallait donc des mécanismes pour corriger automatiquement les facteurs perturbateurs qui altèrent le fonctionnement des machines.
Jusqu’au début des années 1950, les ordinateurs étaient des dispositifs mécaniques ou pneumatiques qui permettaient l’exécution d’algorithmes de traitement plutôt limités et leur connexion aux capteurs et actionneurs était déjà un problème d’ingénierie complexe en soi.
Plus tard, cependant, les systèmes de réglage mécano-pneumatiques ont été progressivement perfectionnés. En fait, ils constituaient la base des systèmes de contrôle chimique et thermique industriels, utilisant de véritables signaux pneumatiques pour leur fonctionnement.
Au début des années 1970, le développement de l’Electronique a permis le développement de cartes à faible coût, de petite taille et faciles à remplacer pour la régulation et le contrôle des vannes et actionneurs.
La nouveauté la plus importante est qu’il était possible de construire un seul produit matériel qui pourrait s’adapter à différentes applications grâce à la modification du logiciel.
Les DCS (Distributed Control System) sont nés pour la gestion des signaux analogiques (pression, température…) et la régulation des procédés chimiques et thermiques . Pour le contrôle des machines et des appareils électriques conventionnels, des appareils ont été développés pour traiter les signaux numériques, dans le but de remplacer les panneaux électromécaniques traditionnels (constitués de relais, temporisateurs, compteurs d’impulsions, etc.) : les automates (Programmable Logic Controllers).
La disponibilité croissante de systèmes de traitement puissants, polyvalents et peu coûteux a permis d’exécuter des fonctions de contrôle de plus en plus avancées ; d’autre part, la simplification de l’échange d’informations entre les différents éléments d’un système d’automatisation, rendue possible par les réseaux de communication et par la disponibilité de capteurs et d’actionneurs « intelligents », c’est-à-dire capables de se connecter directement à un réseau de communication, a permis de simplifier les problèmes de conception, de construction et de gestion d’un système automatisé et, par conséquent, de réduire les coûts.
Au fil des décennies, le développement des technologies de l’information et l’avènement d’Internet ont entraîné une véritable révolution dans les systèmes d’automatisation. Aujourd’hui, en effet, les technologies avancées telles que celles qui supervisent robot pharmacie, les bus de terrain, les capteurs sans fil, l’Internet des objets et la communication autonome entre machines (M2M), le Cloud, l’instrumentation virtuelle, les systèmes cyber-physiques, sont une partie essentielle du monde de l’automatisation. et le contrôle, les capteurs intelligents et les solutions d’intelligence d’usine.